Golbarg (Goli) Razaghi Kashani
Lighting + Electrical

GRK Headquarters
Northeastern United States
BUILDING STATISTICS
Project Team
Architect | Noll and Tam Architects and Planners
Electrical and Mechanical Engineer | Integral Group
Structural and Civil Engineer | KPFF Consulting Engineers
Landscape Architect | BFS Landscape Architects
General Building Data
Building Name | GRK Headquarters
Location | Northeastern United States
Occupancy Type | Commercial/Office
Size | 87200 SF
Levels Above Grade | 2
Project Delivery Method | Design-Bid-Build
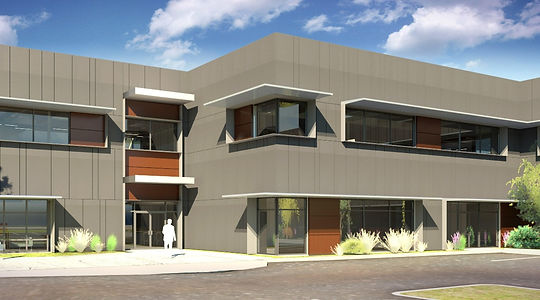
Architecture
The remodeling of this two story office space includes the demolition of the majority of the current building (refer to figure 2); while maintaining the same perimeters and creating a comfortable atmosphere influenced by the current technologies at hand. The demolition excludes part of the first floor but the footprint of the building and the height of the building remain the same after the remodeling. This building is located in the planned development district (zoning) which due to the technology heavy influence on this building there are no historical requirements. The PV panels on the South, West and East side of the building contribute the usage of solar energy as well as an overhang shade for the windows. Lighting wells throughout the building as well as dual pane low-E windows contribute to the energy efficiency of the building.
Sustainable Features
One of the prominent features of the building are the PV panels on the second floor overhang above the window. Daylight is harvested throughout the building from the south facing windows as well as light wells. Photo sensors as well as occupancy sensors and dimmable LED fixtures are installed to ensure energy efficiency. And lastly during the demolition and construction phases all waste will be recycled. The building aims to receive LEED Gold Certification.

Figure 2 - Demolition plan of First Floor
National Models and Codes used for the Remodeled Space
· 2012 International Building Code (IBC)
· 2014 National Electrical Code (NEC)
· 2012 ASHRAE 90.1-2013
· 2014 National Fire Code (NFPA 70)
· 2012 International Energy Conservation Council (IECC)
· 2012 International Green Construction Code (IGCC)
Building Enclosure
Facade | The building is enclosed with weather resistant exterior walls. There are several different exterior wall structures as can be seen in figures 2 and 3, located on the south facing walls. In Figure 3 the Rainscreen is placed to prevent the wall air moisture barrier from getting wet, while collecting the rain water. As part of green building and innovative ideas, the collection of rain water contributes to the LEED Gold Certification.


Roofing | PVC Roofing membrane system will be placed on roof insulation and plywood sheathing as can be seen in figure 4 for the existing structure and figure 5 for the metal framing. The roofing above the roof monitors will have a fully adhered PV systems installed to maximize solar energy gain.
Figure 5 - PVC Membrane Roof Assembly on Existing Structure
Figure 3 - Metal Plate Panel Exterior Wall Assembly
Figure 1 - South Facing Entrance
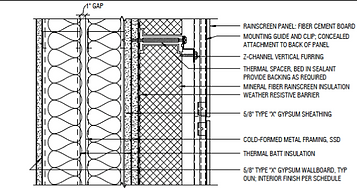
Figure 4 - Rainscreen Exterior Wall Assembly
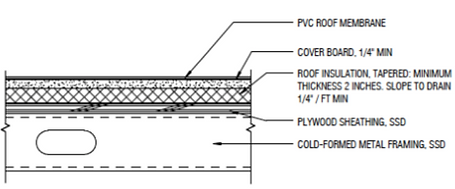
Figure 6 - PVC Membrane Roof Assembly on Metal Framing
All Images are Courtesy of Integral Group & Noll and Tam Architects and Planners
Construction
This building delivery method is Design-Bid-Build, while the building is built in compliance with the code and city permit requirements. The building construction consists of 2 phases, demolition and construction. The demolition consisted of removing the second floor and part of the first floor and most of the electrical and mechanical systems and recycling the material used. The building aims to receive a LEED Gold certification after construction is completed.
Electrical System
The electric utility power feeds the building from the main transformer located outside the building on the North-East corner of the building. The main transformer is a 4000A, 3Ø 4 wire pad mounted transformer feeding the building with a 480Y/277V voltage. The Building utilizes two different utilization voltages of 208Y/120V & 408Y/277V. With the 208Y/120V feeding the receptacles, mechanical, telecommunication and other specialty equipment loads. And the 408Y/277V feeding the lighting and emergency systems of the building.
Lighting System
GRK Headquarters is primary lit with LED fixtures. Direct/indirect pendant luminaires lighting the open offices, direct pendant luminairs lighting the hallways and wall-mounted fixtures lighting the stairwells, bathrooms and atriums. Daylight throughout the building is another source of lighting for the building throughout the day. The lighting is controlled by photocells, occupancy sensors and automated-control roller window shades connected to the daylighting system. Each room is also equipped with dimmer switches to control the light levels from the electrical lights. The exterior walkway is mainly lit by bollards and wall-mounted fixtures lighting the different entrances and the building facade.
Mechanical System
Nine air handeling units (AHU's) and other mechanical equipment including boilers, pumps and condensing units are located on the roof of the building. Multiple fans throughout the building, contribute to the air movement and flow throughout the building and support the mechanical system of the building.
Structural System
This office building comprises of metal plate panel systems, concrete façade structures and weather resistant exterior walls. PVC roofing system will be placed on the plywood sheating roof insulation while PV panels are installed above the roof monitors to maximize solar energy gain. The framing of the building consists of; 30" deep 6' off center steel joists, 5" concrete slab on grade on W24 steel beams as girders and hallow 8x8 steel columns. Hallow steel shapes instead of wide flanges sit on 2x10 purlins on the roof.
Fire Protection System
Heat and Smoke detectors are placed throughout the building. The fire alarm system is remotely connected to the central fire alarm station and in case of fire detection, all alarm sounds and lights will go off to show warning signs. The activation of the heat detectors in sprinkled elevator mechanical room or elevator shaft will cause the disconnect switch to trip and disconnect the power for all the elevator mechanical rooms. The activation of smoke detectors in an elevator lobby, elevator hoistway or elevator machine room will cause the elevator to go to the ground floor unless the smoke detected is from the ground floor then the elevator will go to some other floor.
Transportation
Two elevators located on the West and South-East side of the building and multiple stairwells sum up the vertical transportation through out the building. The roof is accessible through a set of stairs located on the second floor.
Telecommunications
The existing conduits will be used after the demolition. All communications cabling routed in underground conduit will be wet location rated and will either go underground or will be routed in slab on grade. All furniture in the open office have communication connections integrated in the furniture.
Special Systems
Audio/Visual equipment ranging from TV's to projectors can be seen throughout the building in the conference and multipurpose rooms. All of these equipment are powered through the panel boards located on each floor.